BRC
BRITISH RETAIL CONSORTIUM – BRC Certification
A Food Safety Along with
Supply Chain Controls.
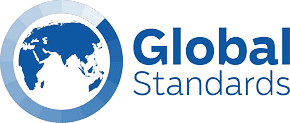
Success through management excellence
BRC Certification – BRC Global Standards is a leading brand and consumer protection organization, used by over 25,000 certificated suppliers over 130 countries, with certification issued through a global network of accredited certification bodies.
BRC Global Standards’ guarantee the standardization of quality, safety and operational criteria and ensure that manufacturers fulfil their legal obligations and provide protection for the end consumer.
BRC supports retailer objectives at all levels of the manufacturing and distribution supply chain. This is achieved through improved supplier standards and consistency in operational controls to avoid product failure.
Implementation and certification to the BRC standards provides concise and documented information to assist with due diligence defense in the event of a direct or indirect food safety incident.
© Global Standards. All rights reserverd for this documented information shared for reading purpose only.
White Paper - BRC
- Food Safety
- Packaging
- Storage and Distribution
- Agents and Brokers
- Consumer Products
- Retail
FOOD SAFETY
BRC Global Standard for Food Safety
The BRC Global Standard for Food Safety is, therefore, developed by food industry experts from retailers, manufacturers, and food service organizations to ensure it is rigorous and detailed, yet easy to understand.
Evolution and Global Establishment
First published in 1998, the Standard is now in its seventh issue and is, furthermore, well-established globally. Additionally, it has evolved with input from many leading global specifiers.
Framework for Managing Product Safety
It, therefore, provides a framework to manage product safety, integrity, legality, and quality, along with the operational controls for these criteria in the food and food ingredient manufacturing, processing, and packing industry.
The BRC Global Standard focuses on:
- The importance of management commitment.
- Hazard analysis and critical control point (HACCP) based food safety programmes.
- Quality management systems.
- Auditing good manufacturing processes – it’s not just a paperwork audit.
- Auditing areas which often have the highest rate of product recalls and withdrawals, such as labelling and packing.
- Developing systems to reduce exposure to food fraud.
- Ensuring consistency of the audit process.
- Providing a BRC Global Standard that is portable enough to allow Additional Modules to be added to reduce audit burden.
- Promoting greater resilience, transparency and traceability in the supply chain.
BRC Covers and Requires:
1. Record Keeping
2. Personnel Qualifications
3. Equipment Verifications
4. Sanitation
5. Cleanliness
6. Process Validation
7. Complaint Handling
White Paper - BRC Retail Consortium certification
PACKAGING
Importance of Packaging
Packaging is, therefore, a fundamental part of any brand. It defines product integrity, security, and drives innovation. Additionally, consumers are attracted to strong and recognisable products that need to be consistent in size, color, and shape. Packaging is, therefore, an integral part of the manufacturing process.
BRC Global Standard for Packaging and Packaging Materials
The BRC Global Standard for Packaging and Packaging Materials is, therefore, the first Packaging Standard in the world to be recognized by the Global Food Safety Initiative (GSFI) benchmarking committee.
Global Acceptance and Certification
It’s why, furthermore, over 3,500 suppliers in over 80 countries have chosen to be certificated to this scheme and it is recommended or accepted by specifiers worldwide.
Versatility of the BRC Packaging Standard
The BRC Packaging Standard can, therefore, be used by any manufacturer producing packaging materials for all types of products – from food to consumer products – at all levels: primary, secondary, and tertiary.
The BRC Global Standard is divided into eight manufacturing technologies:
1. Glass manufacture and forming
2. Papermaking and conversion
3. Metal forming
4. Rigid plastics forming
5. Flexible plastics manufacture
6. Other manufacturing
7. Print processes
8. Chemical processes
The BRC Global Standard consists of six sections:
1. Senior Management Commitment
2. Hazard & Risk Management System
3. Product Safety & Quality Management
4. Site Standards
5. Product & Process Control
6. Personnel
White Paper - BRC Retail Consortium certification
STORAGE & DISTRIBUTION
Introduction to BRC Global Standard for Storage and Distribution
Originally introduced in 2006, the BRC Global Standard for Storage and Distribution, therefore, provides the essential certification link between the range of BRC Global Standards manufacturing Standards and the end user, such as the retailer or the food service company.
Development of the Standard
Developed by multi-stakeholder groups, including industry representatives from certification bodies, food service organizations, and retailers, it, therefore, aims to encompass a wide range of perspectives.
Design and Improvement
The BRC Global Standard is, therefore, designed to reflect best practice and facilitate a process of continuous improvement through a well-designed risk-based product safety management system.
Objective of the Standard
The objective of the BRC Global Standard is to, therefore, ensure that product integrity during storage and distribution is maintained. Furthermore, it aims to uphold customer confidence through audit and certification.
Latest Edition
The third edition of the BRC Global Standard for Storage and Distribution was, therefore, published in 2016.
The BRC Global Standard is divided into eight sections:
1. Senior management commitment and continuous improvement
2. Hazard and risk analysis
3. Quality management system
4. Site and building standards
5. Vehicle operating standards
6. Facility management
7. Good operating practices
8. Personnel
White Paper - BRC
AGENTS & BROKERS
Role of Agents and Brokers
Agents and Brokers (non-manufacturing traders) who buy, sell or facilitate the trade of products, therefore, provide a critical link in the movement and trade of products. Furthermore, they influence supplier product safety and quality standards, as well as being responsible for maintaining an effective chain of traceability.
Framework for Product Safety
The BRC Global Standard for Agents and Brokers has, therefore, been developed to provide a framework for managing product safety, quality, and legality for these non-manufacturing businesses in the food and packaging industries.
THE BRC GLOBAL STANDARD FOR AGENTS AND BROKERS IS AIMED AT:
The BRC Global Standard for Agents and Brokers is, therefore, aimed at the following groups:
Brokers
Brokers: Companies that purchase or ‘take title to’ products for resale to manufacturers, other brokers, retailers, or food service companies, but not directly to the consumer.
Agents or Non-Manufacturing Service Providers
Agents or non-manufacturing service providers: Companies that, therefore, trade between a manufacturer or broker and their customers, but do not own or take title to the goods.
Importers/Exporters
Importers/Exporters: Companies that, furthermore, facilitate the movement of products across national boundaries, satisfying legal and customs requirements. Additionally, importers and exporters may also be agents and/or brokers.
The BRC Global Standard is divided into five sections:
1. Senior management commitment and continual improvement
2. Hazard and risk analysis
3. Product Safety & Quality Management System
4. Supplier & Subcontracted Service Management
5. Personnel
White Paper - BRC
CONSUMER PRODUCTS
The new issue of the Consumer Products Standards Issue 4 in 2016 has, therefore, been fully revised to:
- Recognize the diversity of products included within Consumer Products.
- Additionally, align the Standard with the actual buying expectations of specifiers whilst encouraging continuous improvement.
- Moreover, simplify the requirement and terminology to make it easier to understand.
- Furthermore, widen the scope to include products for wholesale sale and components/raw materials.
- Ensure that requirements are risk-based.
- Additionally, introduce an entry Foundation level and Higher level to encourage continuous improvement.
To achieve these objectives, we have divided Consumer Products into two separate Standards
Global Standard for Consumer Products – General Merchandise
Global Standard for Consumer Products – Personal Care and Household
Each of the Standards can be certificated at either Foundation Level or at Higher level. This enables both flexibilities to reflect customer’s needs depending on the product sector and product / brand risk and provides a clear pathway for continuous development.
The Standards have been developed by groups of industry experts to ensure they are rigorous and detailed but clearly focused on the key issues to produce safe, legal products in accordance with customer quality requirements.
The Standards provide a framework to manage product safety, integrity, legality and quality, and the operational controls for these criteria.
Both Standards focus on
1. The importance of management commitment
2. Product risk assessments to ensure the products design is safe and legal before production
3. Process risk assessment as a tool to ensure that potential issues in the production of the products have been understood, prioritized and effectively managed
4. The design and maintenance of the factory and production environment to ensure this is suitable to manufacture and protect products from contamination
5. An effective product testing and sampling process
The BRC Global Standard is divided into seven sections:
1. Senior management commitment
2. Product risk management
3. Product Safety & Quality Management System
4. Site Standards
5. Product inspection & testing
6. Process control
7. Personnel
White Paper - BRC
RETAIL
Introduced in 2016, the BRC Global Standard for Retail provides essential certification for organizations that retail food products, as well as hard lines. The BRC Global Standard covers the activity of retailing, as well as commissary, sourcing and in-store production.
Retailers are the last step in the food supply chain prior to the consumer and play a critical role in managing the supply chain, as well as the delivery of goods and services to the consumer.
This BRC Global Standard is, therefore, designed to promote best practice on product safety, quality and the operational criteria required to fulfil obligations with regard to legal compliance and consumer protection.
The BRC Global Standard for Retail has been developed to provide a framework for businesses to manage the safety, quality and legality of products and services offered in the retail setting.
Therefore, the Standard is aimed at:
- Organizations that retail food products
- The sourcing and supplier approval program
- In-store preparation and processing
The BRC Global Standard is divided into seven sections:
1. Senior Management Commitment & Continual Improvement
2. The Food Safety Plan
3. Product Safety & Quality Management System
4. Facility & Operational Standards
5. Product Controls
6. Process control
7. Personnel
White Paper - BRC
Benefits of BRC
- It, therefore, enhances integrated requirements of quality, environment, health, supply, and food safety.
- Additionally, controlled conditions are maintained in order to prevent cross-contamination of food and its supply chain.
- Moreover, manufacturing processes are clearly defined and controlled. All critical processes are validated to ensure consistency and compliance with specifications.
- Furthermore, manufacturing processes are controlled, and any changes to the process are evaluated. Changes that impact the quality of the food are validated as necessary.
- Instructions and procedures are, therefore, written in a clear and unambiguous manner.
- Moreover, operators are trained to carry out and document procedures.
- Additionally, records are made, manually or by instruments, during manufacture to demonstrate that all the steps required by the defined procedures and instructions were, in fact, taken and that the quantity and quality of the food were as expected. Deviations are, therefore, investigated and documented.
- Furthermore, records of manufacture (including distribution) that enable the complete history of a batch to be traced are retained in a comprehensible and accessible form.
- Additionally, the distribution of the food minimizes any risk to its quality.
- Moreover, a system is available for recalling any batch from sale or supply.
- A sufficient reason to, therefore, get the maximum client-age on behalf of BRC implementation.

© Global Standards. All rights reserverd for this documented information shared for reading purpose only.